OEM Supply Granulation System - Embossed Metal Composite Exterior Panels Production Line – Amulite
Short Description:
Product Detail
Product Tags
Related Video
Feedback (2)
OEM Supply Granulation System - Embossed Metal Composite Exterior Panels Production Line – Amulite Detail:
1. Wall Panel Introduction
Embossed Metal Composite Exterior Panels Production Line is the production of new-type environmentally-friendly lightweight building materials that are currently popular in the world. and decorative wall panels based on polyurethane foam. It can produce fire-retardant thermal insulation decorative wall panels with steel plate on the surface. polyurethane in the middle. and aluminum foil or steel plate on the bottom.The main application areas of the products: renovation of old buildings. high-end villa apartments. villas. hotels. light steel structures. mobile houses. farmhouses. large shopping malls. interior and exterior walls of factories. etc.
2. Equipment Composition
Embossed Metal Composite Exterior Panels Production Line Main Unwinder→ Embossing Machine→ Leveling Machine→ Side Forming Machine→ Heating Platform→ AB Foam Machine Injection→ Aluminum Chain Plate Laminating Machine→ Saw Board Cut Off→ Coloring→ Packing Etc.
3. Embossed Metal Composite Exterior Panels Production Line Main Technical Parameters
Wall Panel Specification:A. 380×16mm B. (380-500)×(30-40)mm
Production Speed:4-10m/min
Length Of Aluminum Alloy Double Crawler:18-24m
Total Power Of Equipment:About 60Kw
Production Line Capacity:About 1. 000. 000Sq.m.
4. Embossed Metal Composite Exterior Panels Production Line Introduction Of Unit Structure And Function
Ⅰ. Unwinder
Function:Used For Unwinding And Embossing Of Steel Coils
Structure Type:Section Steel Welding Frame. The Lateral Displacement Is Realized By Hydraulic Cylinder. Prevent Deviation Of Coil Material. Unwinding Adopts Passive Type. Have Pneumatic Brake For Tension Control.
Ⅱ. Embossing Machine
Function:According To Different Patterns Of Wall Panel. Two Opposite Embossing Metal Rollers Are Used To Press Different Patterns Of Color Steel.
Ⅲ. Foaming Machine:
BLC(R)Type Low Pressure Continuous Foaming Machine Or PH(R/F) High Pressure Foaming Machine. Use 1 Resin (A) Tank. 1个Curing Agent (B) Tank;The Two Metering Pump Units Are Driven By Independent Variable Frequency Motors. The Output Flow Of Metering Pump Is Controlled By Changing The Speed Of Metering Pump。Finally. The Components Are Mixed According To The Required Ratio And Evenly Sprayed Between The Lower Steel Plates Or Other Substrates.
Ⅳ. Forming Machine
Function:The Shape Of Embossed Color Steel Was Treated By Multi Wheel Flanging.
Ⅴ. Laminator
Function:Complete Online Foaming And Shaping Of Polyurethane;The Chain Plate Unit Is Composed Of Drive Motor. Chain Wheel. Aluminum Alloy Chain Plate. Pin Shaft And Rolling Bearing. Using Electric Heating Tube Heating Method;It Can Quickly Heat The Double Belt Machine To The Required Temperature For Production。When The Temperature Reaches The Preset Value. The Electric Heating Can Be Turned On Or Off According To The Actual Situation.
Ⅵ. Fixed Length Sawing Machine
Function:Saw The Formed Board According To The Set Size.
Function:The Base. Fuselage And Upper Movable Frame Adopt Section Steel And Plate Welding Structure. Connected By Linear Guide Rail. The Mounting Surface Of Guide Rail Is Finished. Ensure Installation Accuracy;The Sawing Motor Is Installed On The Upper Moving Frame. The Moving Frame Is Driven By A Geared Motor. Lateral Movement;The Clamping Device Is Installed On The Body. It Is Composed Of Air Cylinder And Pressing Block;The Reset Device Is Composed Of A Cylinder And A Buffer Device;When The Plate Reaches The Set Length. The Clamping Cylinder Pushes The Clamping Block Down. And The Reset Cylinder Pushes The Body To Move With The Plate; At The Same Time. The Sawing Motor Is Started. And The Reduction Motor Drives The Upper Moving Frame To Move Horizontally. So As To Realize The Transverse Cutting Of The Plate; After The Cutting Is Completed. The Clamping Device Is Lifted. And The Reset Cylinder Drives The Body To Return To The Original Point To Reset.
5. Embossed Metal Composite Exterior Panels Production Line Automatic Control
The Automatic Control System Is Divided Into Four Parts: Unwinding And Embossing Area Control. Forming And Lamination Area Control. Foaming Area Control And Sawing Area Control. The Total Power Is About 60KW;The Heating Platform Is About 30KW. The Whole Control System Consists Of Programmable Controller. Test Switch. Delta Inverter Driver And Other Components. Through The Touch Screen Parameter Input And Button Cooperation Operation. Realize The Automated Production Of The Production Line. Its Performance Is Reliable And Stable. And The Operation Is Simple And Easy.
Product detail pictures:
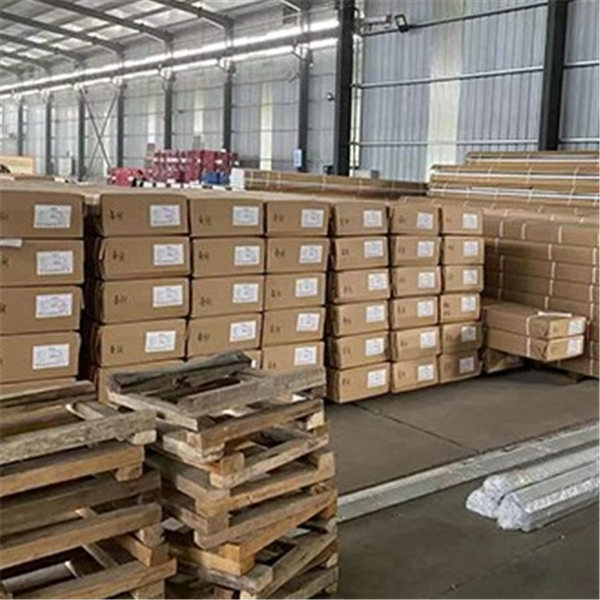
Related Product Guide:
Our merchandise are broadly identified and trusted by end users and can satisfy continually developing economic and social requires for OEM Supply Granulation System - Embossed Metal Composite Exterior Panels Production Line – Amulite, The product will supply to all over the world, such as: Portland, Saudi Arabia, Afghanistan, Our business activities and processes are engineered to make sure our customers have access to widest range of products with the shortest supply time lines. This achievement is made possible by our highly skilled and experienced team. We look for people who want to grow with us around the globe and stand out from the crowd. We have people who embrace tomorrow, have vision, love stretching their minds and going far beyond what they thought was achievable.

The factory technical staff gave us a lot of good advice in the cooperation process, this is very good, we are very grateful.
