OEM Customized Fiber Cement Board Machinery Manufacturing Plant - Calcium Silicate Board /Fiber Cement Board Production Line – Amulite
Short Description:
Product Detail
Product Tags
Related Video
Feedback (2)
OEM Customized Fiber Cement Board Machinery Manufacturing Plant - Calcium Silicate Board /Fiber Cement Board Production Line – Amulite Detail:
With Fiber Cement Board Products Wide Usage In Building And Decoration Industry,Fiber Cement Board Production Line Technology And Automatic Level Always Keep Upgrading All The Time.With Continuous Effort Of Amulite Engineers Team We Always Keep Technology Innovation And Make Our Fiber Cement Board Machinery Be ln Higher Level In World Cement Board Products Market ;Now We Have Regular Manufacturing And Supply Fiber Cement Board/Calcium Silicate Board Production Line With Capacity 3Million Sq.m Per Year. 4Million Sq.m Per Year. 6Million Sq.m Per Year ,8Million Sq.m Per Year,10Million Sq.m Per Year Regularly;Standard Board Size 2440X1220X(4-25)MM And 3000X1220X(4-25)MM,Also We Can Customize Manufacturing Equipment According To Customers’ Requirement,Any Customized Specification Can Be Realized;
Types And Features
Fiber Reinforced Calcium Silicate Board/Fiber Cement Board Also Call As CSB/FCB Board.As New Type And Environmental Protection Building Materials ,Which Has Advantage Of Light Weight.High Strength,Fireproof,Good Heat Insulation Performance.Wide Usage And Long Lifetime Etc .Now Calcium Silicate Board/Fiber Cement Board Products Are Widely Used In Building Ceiling And Partition.High Building’s Exterior Insulation ,Public Building Fireproof Panels,Ceiling Tiles,Air Duct.Ship Partition Panels And Fire Escape Path Inside Buildings Etc;
Production Technology
Calcium Silicate Board/Fiber Cement Board Take Inorganic Fibers Or Cellulose Fiber As Fiber Reinforced Materials.Take Calcium And Silicate Materials As Main Cementing Materials.With Production Process Slurry Mixing,Board Forming.Board Stacker,Pre-Curing,Demold Template,Autolave Curing To Produce Out,For Some Higher Standard Board Requirement.Can Add Board Press,Board Drying,Board Sanding And Edge Trimming Process,And Make Painting On Face To Improve Board Standard And Usage , Then Can Increase More About Board Added Value And Enlarge Board Sales Market ; For Forming Board Process Of Calcium Silicate Board/Fiber Cement Board Production Line Normally Takes Flow-On Slurry Forming Type,Hatchek Forming Type And Extrusion Type .
Main Raw Materials
Reinforced Fiber (Kraft Paper Pulp,Wollastonite,Glass Fiber.Mica Etc),Silicate Materials (Quartz Sand,Fly Ash, Diatomite Etc},Calcium Materials(Lime Powder, Cement),Additives Etc
Products Standard.
Calcium Silicate Board Industry Standard JCIT564-2008<F1ber Reinforced Calcium Silicate Board Standard> Fiber Cement Board Industry Standard JCIT 412.1-2006<Non-Asbestos Flat Fiber Cement Board Standard >
Production Process introduction
1.Water Tank And Cement Tank Process
There Is One Clean Water Tank And One Muddy Water Tank ;Both Water Tank Body Is Welded By Carbon Steel,The Muddy Water Tank Is Used To Collect Back The Recycle Water From Sheets Production Process,Muddy Water Take To Mix Into Slurry Process ,For Clean Water Tank Is Used To Take Clean Water To Clean Felt And Net Cage Normally.
2.Paper Pulp Process
Paper Pulp Process Includes Paper Shredder Machine,Refiner,And Paper Pulp Storage Tank
Paper Shredder Is Used To Shredder The Kraft Papers
Refiner Used To Grind The Paper Pulp To Be Slurry And Pumping Them To The Paper Pulp Storage Tank.
Paper Pulp Storage Tank Is Used To Store The Paper Pulp.
3. Flow-On Slurry Vacuum Water Dehydration Process
Can Choose Flow-On Slurry Forming Sheets System Or Hatschek Types Forming Sheets System To Form Sheet,We Can Customize According To Customers’ Requirement.
Well Mixed Slurry Flow Into Flow-On Slurry Box,Then From Slurry Box Convey To Running Felt To Form Slurry Layer,With Vacuum Dehydration And Chest Roller Press To Form Sheet Layer,After Layers Rolling Round Forming Sheets Drum Roller ,Then With Automatic Cutting To Form Flat Wet Sheets .
Air-Water Separator :It Is Used To Separate The Steam Water Mixture Extracted From The Vacuum Box, Flow Into The Collecting Well, And The Air Is Pumped Back To The Vacuum Pump.
4.Flow-On Slurry Sheet Forming Process
After Forming Roller Forming Sheets,Then With Automatic Laser Positioning And Cutting ,Whole PC Of Wet Sheets Go Into Convey Process.
5.High Pressure Water Cutting System
This High Pressure Water Cutting System Is Our Own Patent Equipment,With Imported High Pressure Water Pump To Make High Pressure Water To Make Tidy Cutting Of Wet Sheets On Conveyor.
6.Forming Wet Sheet And Wet Sheet Conveying Process
This Process Is Used To Convey The Cut Well Wet Sheet From Forming Roller Convey The Wet Sheets To Position And Make Automatic Edge Cutting .
7. Automatic Stacker
Two Sheets Can Be Stacked At One Time. The Suction Cup Sucks Up The Wet Sheets From Receiving Conveyor machine And The Template On The Trolley At Another Working Position, And Then Stacks Them On The Trolley At The Middle Position(With The Vacuum Suction Of High-Pressure Fan). The Accurate Movement Of The Suction Cup Is Realized By The Gear On The Swing Arm Pushed By The Hydraulic Push Rod.
PLC Control, Automatic Operation.
Function: the Automatic Stacker Is Used To Sort And Stack The Quality And Inferior Products Of Fiber Cement Board/Calcium Silicate Board.
The Products Are Stacked Orderly And Highly Automated, Which Will Effectively Improve The Production Efficiency.
8 .Press Machine
Press Machine Is Used To Increase The Density And Strength Of Products ,
Standard Pressure:7000ton, Press Table Size: 1350 * 2700/3200mm, Spacing: 1200mm, Working stroke: 400mm, Pressure Speed: 0.05 ~ 0.25mm/s ;
Return Speed: 15 mm / S
In And Out Of Press Transport Car: One Unit.
Power: 27.5kw
9.Trolley Traction System
Allowable Load: 20T
Table Rail Inner Distance: 750mm
Walking Mechanism:
Reducer Model: fa67-60-y-1.5, I = 50
Matching Motor Speed: 1380r / min, Power: 1.5kw
Traveling Speed Of Trolley: 9m / min
10. Vacuum Demoulding Template Machine
The Movement Of The Car And The Rise And Fall Of The Suction Cup Are Controlled By The Servo Motor.
The Demoulding Template machine Separates The Template And The Sheets On The Trolley, The Template Is Put On The Oil Brush Machine To Brush Oil, And The Sheets Is Piled On The Other Side Trolley. Add One Autoclave Interleave Spacer For Every 150 mm Sheets.
The Accurate Movement Of The Suction Cup Is Realized By The Gear On The Swing Arm Pushed By The Pneumatic Push Rod.
PLC Control, Automatic Operation.
11.Autoclave Process
Due To The Characteristics Of Fiber Cement Board/Calcium Silicate Board, Lime And Quartz Sand Powder Are Used As The Main Raw Materials In The Production Process, Which Needs To Get Chemical Reaction Under High Temperature And Higher Pressure Environment,Can Let All Raw Materials Mixed Enough Well,And Make The Sheets Better Hardness And Strength.
12.Boiler
In The Production Process Of Fiber Cement Board/Calcium Silicate Board,Autoclave And Dryer Are Used For Processing, And
The Heat Energy Of Autoclave And Dryer Is Supplied By Boiler!
13. Dryer
It Is Used For Drying Fiber Cement Board/ Calcium Silicate Board ,After Autoclave Curing ,The Moisture Content Of Fiber Cement Board Is About 25%. Before Sanding, Edging And Chamfering, The Moisture
Content Should Be Reduced To Lower Than 15% By Dryer. The Dryer Has The Advantages Of High Production Efficiency, Beautiful Appearance, Convenient Maintenance And Easy Operation.
14. Edging Trimming System
The Edge Trimming Machine Is Mainly Composed Of Sheets Feeding Roller Table,Longitudinal Edge Trimming Machine, Steering Table, Transverse Edge Trimming Machine,Sheets Discharging Roller Table, Electric Cabinet, Air Cabinet, Etc;
Edging Trimming Machine Is Used To Make Edging And Trimming Of Fiber Cement Board,Then Stacking To Be Finished Products.
Product detail pictures:
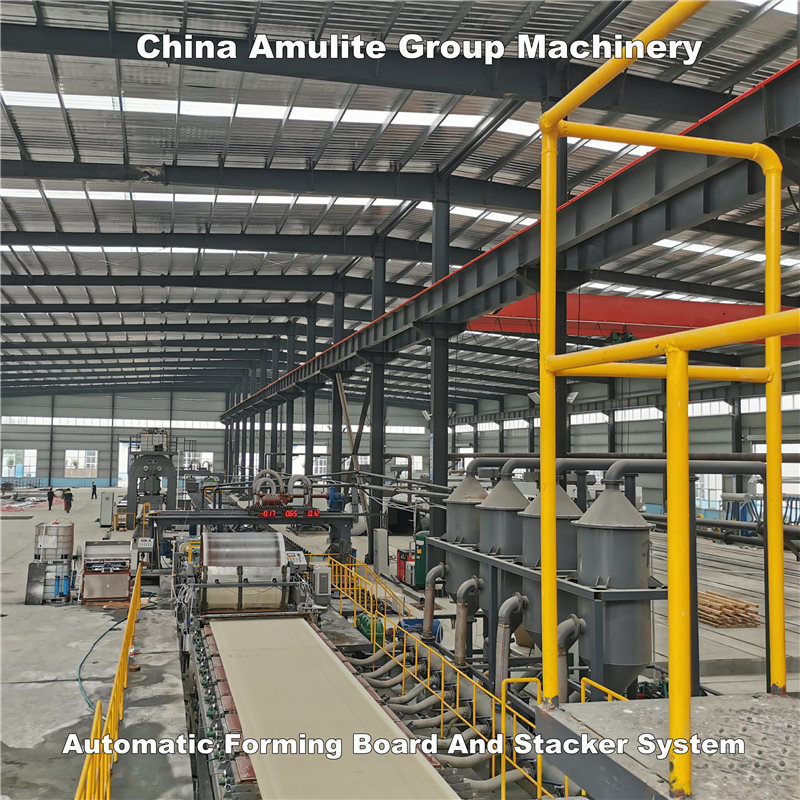
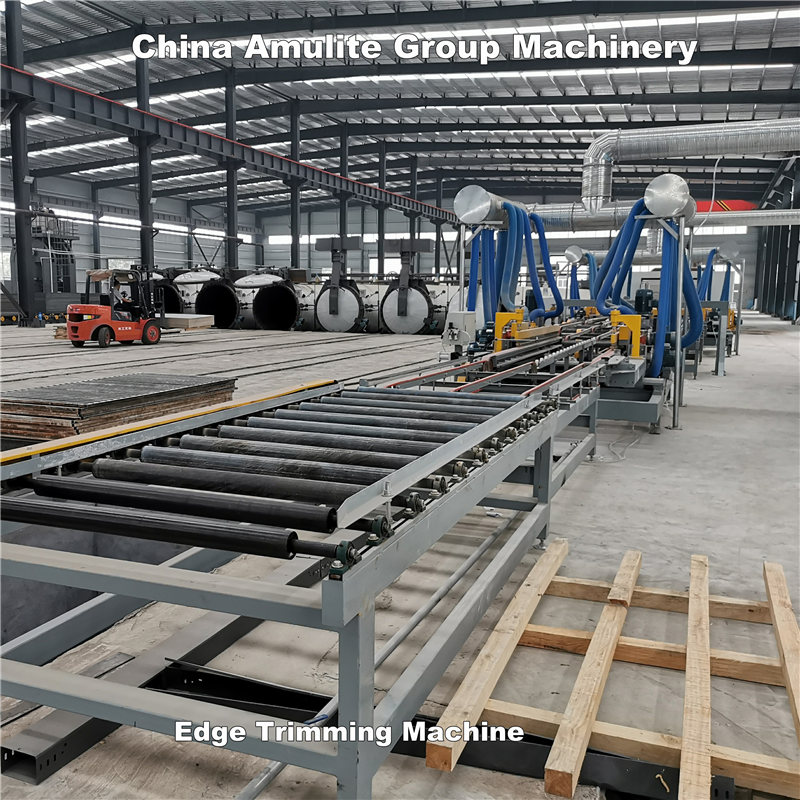



Related Product Guide:
"Based on domestic market and expand abroad business" is our progress strategy for OEM Customized Fiber Cement Board Machinery Manufacturing Plant - Calcium Silicate Board /Fiber Cement Board Production Line – Amulite, The product will supply to all over the world, such as: Benin, Wellington, Singapore, We look forward to hearing from you, whether you are a returning customer or a new one. We hope you will find what you are looking for here, if not, please contact us immediately. We pride ourselves on top notch customer service and response. Thank you for your business and support!

This supplier stick to the principle of "Quality first, Honesty as base", it is absolutely to be trust.
