Amulite CO2 XPS Foam Board Production Line
Short Description:
I.Technical Introduction
First,compounding symmetrical1y XPS material with other assistant materialslike nucleant agent and color batch;Secondly put them into hopper of Grade Iextruder by vacuum feeder automatical1y;Thirdly melting and plasticizing resin byspecial1y designed screw symmetrically,at the same time injecting foam agent byhigh pressure and mixing it with melted resin;Fourthly,putting them into Grade IIextrusion system to meit,mix, add pressure and cool again and extruding foam boardby special mould for board, then cooling and forming board by cooling and formingdexiss..kifthly. putting the board into Grade I draw-off system and transporting theminto Grade Il draw-off system by transportation rol1s; Sixthly , cutting waste edge bysaw of both-side and finishing transverse cutting according to set 1ength; the 1ast step,stacking and storage.
Product Detail
Product Tags
Electricity Unit:
Main motor Beide Brand (Siemens Standard Motors Ltd.)
Transducer Danfoss or Siemens Brand
AC Contactor Siemens or Schneider Brand Temperature controller meter Omron Brand or Fuji Brand Voltage 380V,50HZ
AM-XPS75P/200 CO2 XPS Foam Board Production Line
I. Technical Introduction
First, compounding symmetrically XPS material with other assistant materials like nucleant agent and color batch; Secondly put them into hopper of Grade I extruder by vacuum feeder automatically; Thirdly melting and plasticizing resin by specially designed screw symmetrically, at the same time injecting foam agent by high pressure and mixing it with melted resin; Fourthly, putting them into Grade II extrusion system to melt, mix, add pressure and cool again and extruding foam board by special mould for board, then cooling and forming board by cooling and forming device;Fifthly, putting the board into Grade I draw-off system and transporting them
into Grade II draw-off system by transportation rolls; Sixthly, cutting waste edge by
saw of both-side and finishing transverse cutting according to set length; the last step, stacking and storage.
II. The Main Material
1> XPS resin
2> Foam agent & assist foam agent 3> Nucleant agent
4> Color batch
5> Other assistant materials
Note: We will provide our customers with material prescription, material type and relative technical documents after signing a contract.
Machine Component
1> Plastic mixer 1 set
2> Grade I extrusion system 1 set
3> CO2 foam agent injection system 1 set 4> Assistant foam agent injection system 1 set 5> CO2 flow show system 1 set 6> HCFC Foam agent injection system 1 set 7> Automatic net-exchange system 1 set
8> Grade II extrusion system 1 set
9> Extrusion die head 1 set
10> Calibrating and draw-off system 1 set
11> Transmission and cooling system 1 set
12> Grade II draw-off system 1 set
13> Lengthways cutting system 1 set
14> Horizontal cutting system 1 set
AM-75P/200 CO2 XPS Foamed Board Production Line
1. Feeding system
2. AM75/44 Twin-screw extruder 1 set
3. CO2 foam agent injection system1 set
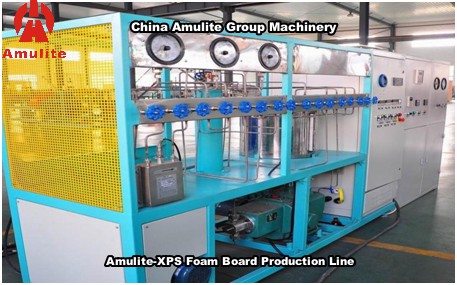
4. Assistant foam agent injection system 1 set
5. Freon Foam agent injection system 1 set
6. CO2 flow show system 1 set
7. Automatic net-exchange system 1 set
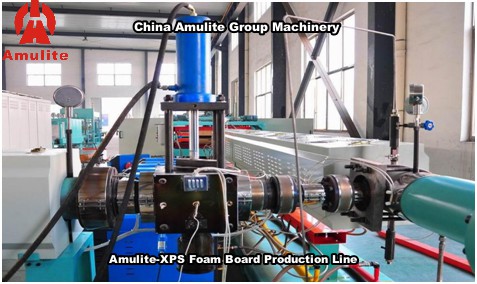
8. Grade II extrusion system 1 set
9. Extrusion die head 1 set
10. Calibrating and draw-off system 1 set
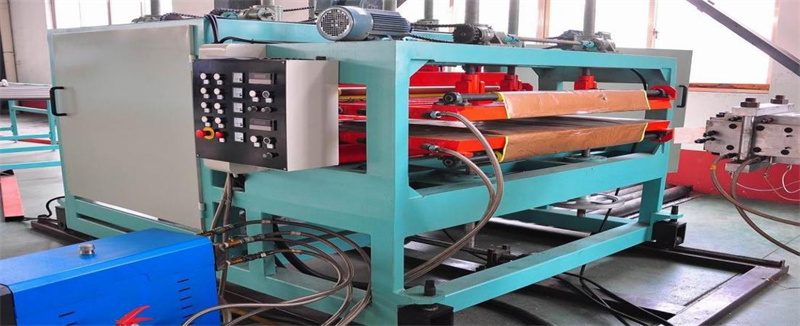
11. Transmission and cooling system 1 set
12.Grade II draw-off system 1 set
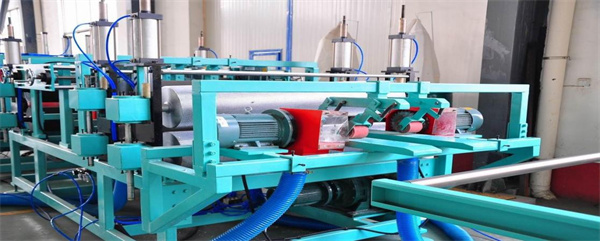
13. Lengthways cutting system 1 set
14. Horizontal cutting system 1 set
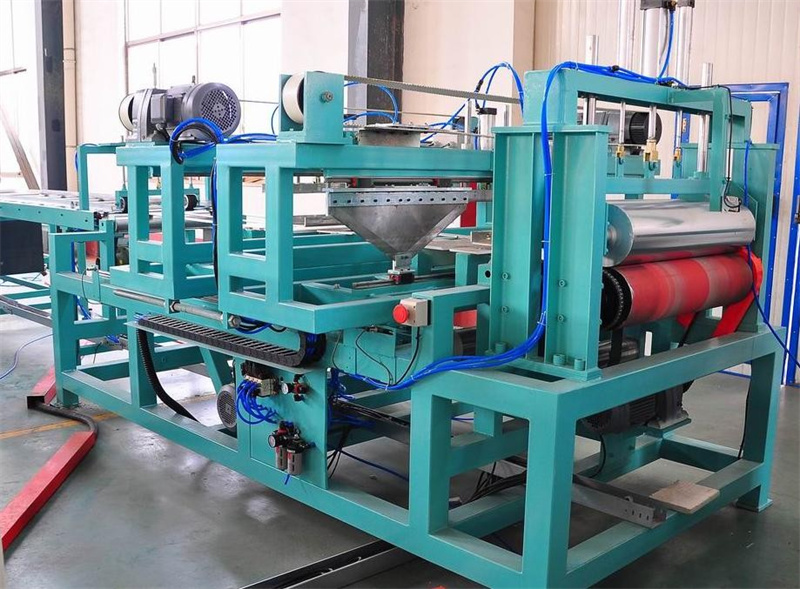
15> Transverse cutting system 1 set
15. Electricity unit
XPS Foamed Board Recycling and Pelletizer Machine
Model AM-XPS-JR100B
1> XPS foam board crusher device 1set
2> Single screw plasticizing and extrusion device 1set
3> Filter net-changing device 1 set
4> Cooling tank 1 set
5> Cutting pellet machine 1 set
Note: The above proportion of foam agent is just for your reference, the actual data is adjusted according to the demand of raw material and market.